FORKIT - Nutritious Meals, Packaged Faster and Longer Lasting
In just 2 years, FORKIT has grown from a lockdown-lifestyle pivot to a fully-fledged food producer.
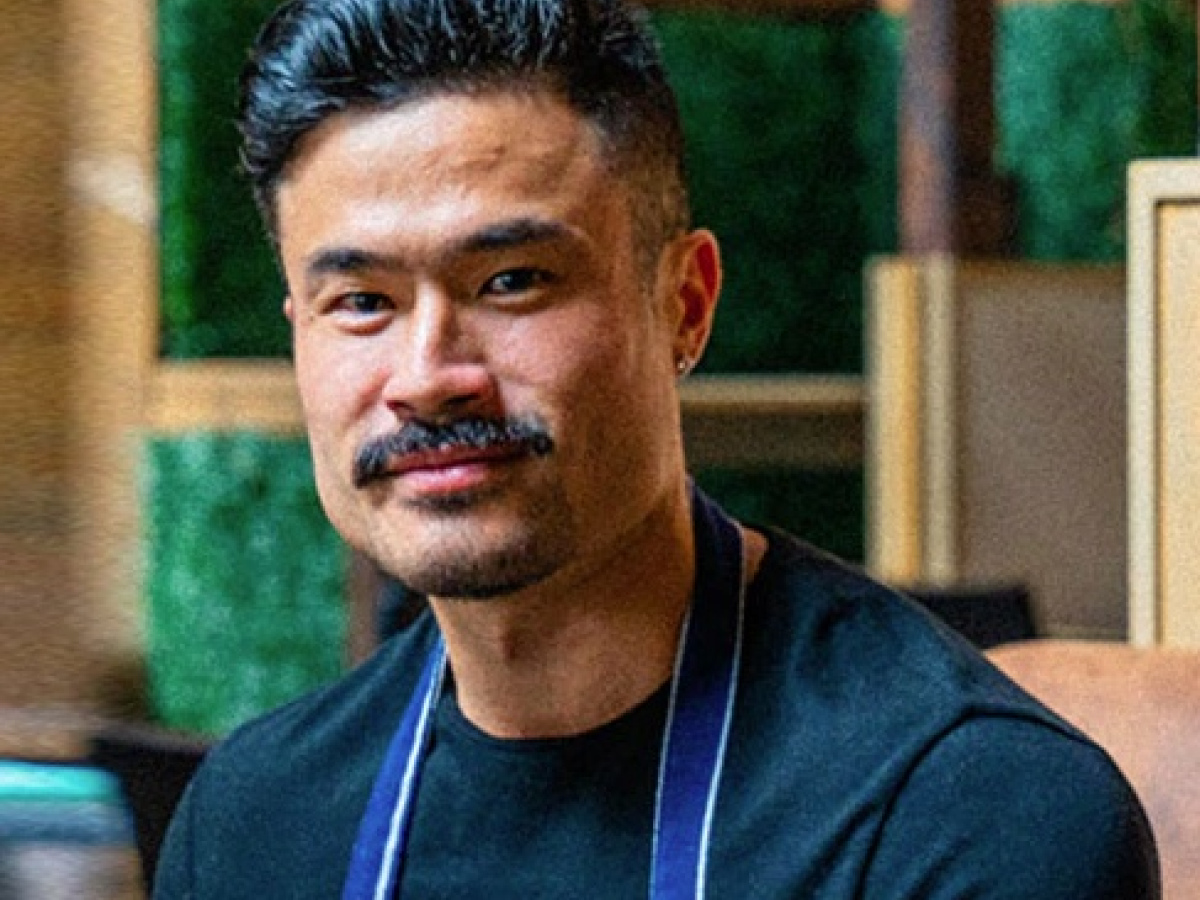
When the 2020 lockdown hit, personal trainer Brian was cut off from his customers. This innovative Kiwi realised that, while his clients couldn’t train with him in person, he could help them stay on track with healthy meals.
Combining his passion for nutrition this his tongue-in-cheek sense of humour, FORKIT was born. Brian set out with the mission of helping people achieve their fitness goals through forkin’ delicious, macro and micro-nutrient balanced pre-made meals, delivered to the doorstep.
Starting out, Brian kitted their production kitchen out with a semi-automatic, single-cavity tray sealer and home-compostable food trays. The set up was a great entry point, but as it turned out, the guys were really onto something…
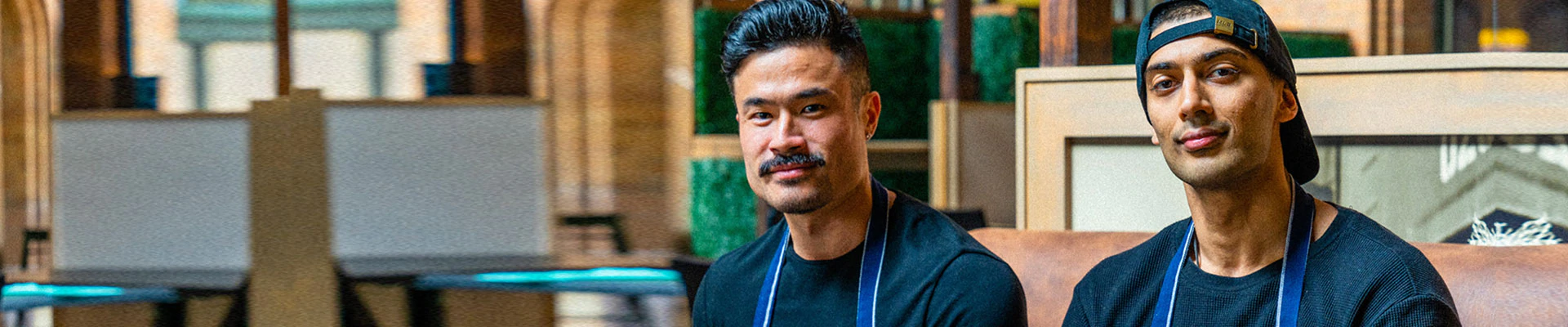
Contour’s meal-delivery packaging magician, Naomi Moxham, had been working with FORKIT since day one, so when Brian looked for advice on how to take on the next phase, he gave Naomi a call.
“Brian needed a solution that helped them increase output and extend the shelf life of their packaged products, without sacrificing their sustainability values”, said Naomi. “I had a pretty clear idea of how we could help.”
Armed with experience and inside knowledge, Naomi recommended a change of equipment, consumables and packaging process.
An automated, two-cavity tray sealer tackled two birds with one stone.
The END-900 tray sealer allowed the guys to seal two trays at the same time, with a much faster sealing cycle time. This upgrade saw packaging speed increase 4-fold.
Better still, this tray sealer made MAP-Sealing possible. MAP, or modified atmosphere packaging, surrounds the portioned food with an inert gas before sealing. Removing oxygen and regular air from the sealed product significantly slows down the rate of oxidation and spoilage. This technology had the potential to double shelf life, but it relied on one final piece of the puzzle.
Driven by sustainability values, FORKIT had been using home compostable food trays. These are a fantastic option for relatively fast consumption products, but their material composition is not suitable for gas-flushing. “To put a long story short, they would let normal air back in” says Naomi.
So, Naomi and the Contour team suggested a shift to CPET trays. Made largely from recycled content, and kerbside recyclable in New Zealand, the shift to CPET trays meant FORKIT had the final piece in the puzzle. The CPET trays + gas flush meant products that last longer in their customer’s fridge and gave FORKIT more flexibility for production scheduling.
Faster sealing. Longer shelf life. More Flexibility and no compromise on sustainability.
Job done.
Starting out, Brian kitted their production kitchen out with a semi-automatic, single-cavity tray sealer and home-compostable food trays. The set up was a great entry point, but as it turned out, the guys were really onto something…
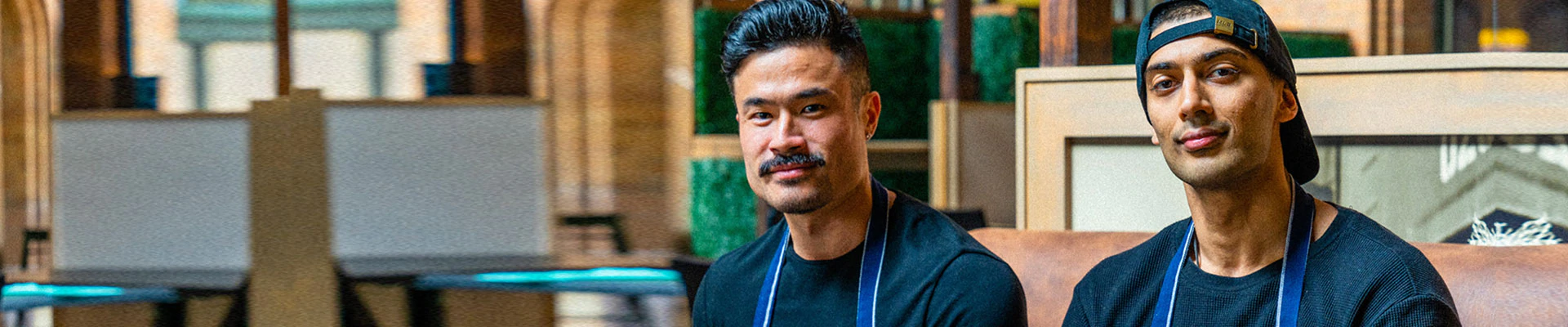
Gearing up for growth
Business blossomed and the team needed to increase production capacity, production flexibility and deliver longer lasting products.Contour’s meal-delivery packaging magician, Naomi Moxham, had been working with FORKIT since day one, so when Brian looked for advice on how to take on the next phase, he gave Naomi a call.
“Brian needed a solution that helped them increase output and extend the shelf life of their packaged products, without sacrificing their sustainability values”, said Naomi. “I had a pretty clear idea of how we could help.”
The right tools for the job
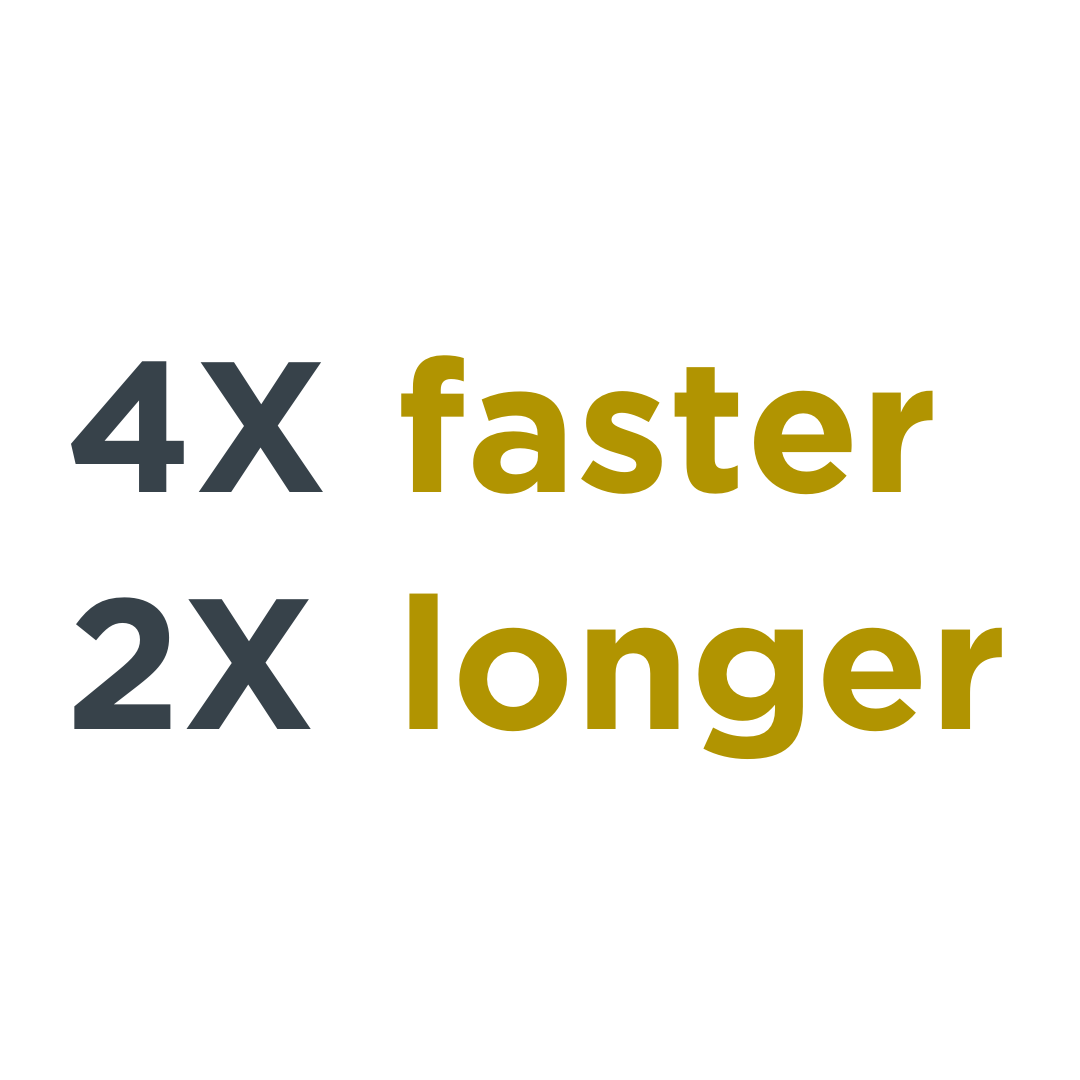
An automated, two-cavity tray sealer tackled two birds with one stone.
The END-900 tray sealer allowed the guys to seal two trays at the same time, with a much faster sealing cycle time. This upgrade saw packaging speed increase 4-fold.
Better still, this tray sealer made MAP-Sealing possible. MAP, or modified atmosphere packaging, surrounds the portioned food with an inert gas before sealing. Removing oxygen and regular air from the sealed product significantly slows down the rate of oxidation and spoilage. This technology had the potential to double shelf life, but it relied on one final piece of the puzzle.
So, Naomi and the Contour team suggested a shift to CPET trays. Made largely from recycled content, and kerbside recyclable in New Zealand, the shift to CPET trays meant FORKIT had the final piece in the puzzle. The CPET trays + gas flush meant products that last longer in their customer’s fridge and gave FORKIT more flexibility for production scheduling.
Faster sealing. Longer shelf life. More Flexibility and no compromise on sustainability.
Job done.